A customized laser welding machine for aviation body skins generally entails a high-precision, automatic system made for joining lightweight steel alloys like light weight aluminum and titanium, frequently incorporating attributes like robot arms, specialized welding heads, and vision systems for exact alignment and quality control. These equipments are developed to deal with the complicated geometries of airplane fuselages, decrease distortion, and boost manufacturing effectiveness while keeping high weld high quality and structural honesty. In this piece, we dig into why a tailor‑made Laser Welding Machine for Aviation Fuselage Skin makes sense.
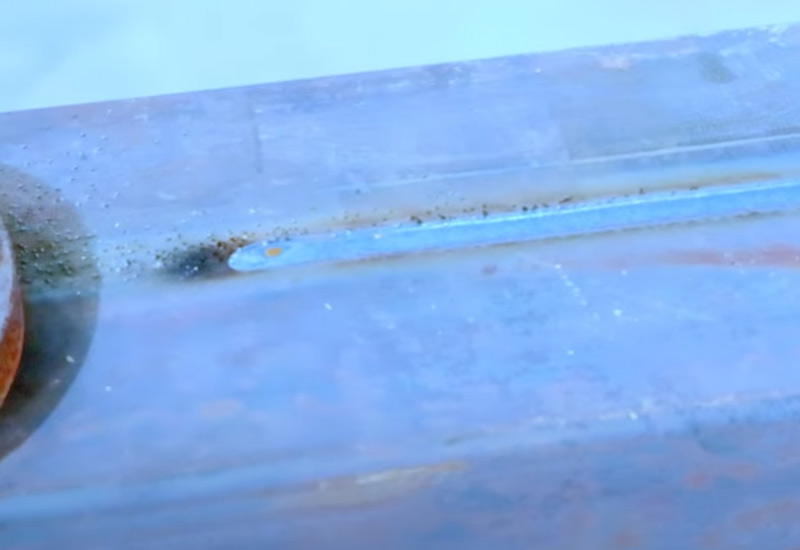
Why Fiber Laser Tech Outshines Rivets
Gone are the days when riveting was king. Fiber lasers offer pinpoint heat input. You melt metal only where you need. That means you avoid the bulk of fasteners. You cut assembly time. You dodge post‑weld rework. At BOGONG Laser, our rigs nail alignment. They run with photodiode feedback and tight spot control. That slashes common fusion glitches and lack‑of‑fusion headaches.
Precision that Keeps Skin Intact
Weld penetration matters. You want just enough melt—deep enough to secure panels but shallow enough to avoid warping. Studies show that matching typical skin thickness keeps seams clean and mechanical strength well above safety specs . Hitting that sweet spot narrows the heat‑affected zone, prevents distortion, and ensures the joint meets the toughest flight‑readiness standards .
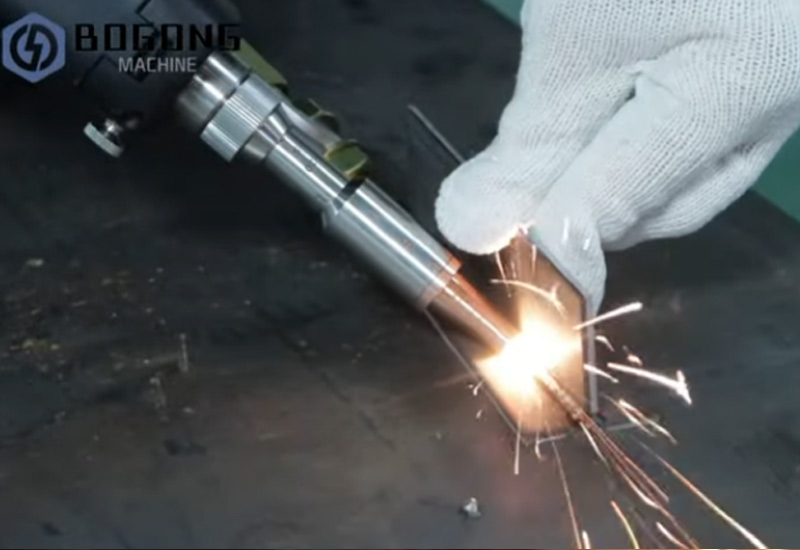
Reduced Thermal Footprint
Aluminum’s thermal conductivity is no joke. It wicks heat away fast. Left unchecked, you get hot spots or burn‑through. With dynamic focus control and slight beam offsets, you follow the panel contour closely. Online photodiode monitoring flags any drift in real time. You tweak beam power on the fly. The outcome? A tiny thermal footprint, consistent metallurgical structure, and no surprise porosity.
Tackling Aluminum: Reflectivity and Heat Sink
Aluminum’s reflectivity is a double‑edged sword. You need a powerful burst to pierce the surface. But back‑reflections can zap fiber optics. Our laser heads sport reinforced optics and beam dumps. That cuts downtime. Plus, smart pulse modulation keeps spatter in check. No more grinding down burrs after the fact.
Spot Position and Angle Matter
A tiny shift in beam angle changes weld profile big time. Industry best practice aims for an angled approach on skin panels. And a slight lateral offset from exact center helps tame fusion depth . BOGONG Laser rigs let you dial that in via touchscreen. They store presets per alloy. You don’t need to be a welding guru—just pick the right program.
Real‑Time Vision Feedback
CCD camera integration watches the melt pool. It tracks pool oscillation and flags pore formation early. You dodge porosity. You also get data logs for SPC (Statistical Process Control). That’s how you hit near‑perfect consistency on the shop floor.
Building for Big Panels: Gantry vs. Robot
Aircraft skins can stretch across multiple meters. You need a system built for that span. Two flavors dominate: gantry‑based and robotic arms. Each packs its own perks.
CNC Gantry Systems at Scale
Gantry rigs deliver rock‑steady straight‑line motion. You mount dual fiber heads and sync scans. Add FEA‑driven weld sequencing and you slash clamp marks and distortion. It handles massive wing panels with ease.
Robot Welders for Complex Contours
Sometimes panels curve. A gantry won’t cut it. Robot arms with full‑range joints fill that gap. They swing the head along contoured paths. They deliver quicker cycles on tricky geometries. BOGONG Laser’s robot solution pairs with seam‑tracking lasers. The arm adapts on the fly. It masters convex and concave surfaces alike .
Please click on the video below to watch the specific operation.
Dual Positioner Robotic Arm Welding Machine | Double Positioner Tig Robot Welder
Real‑World Snapshots
Airbus A318 Wing Panel Retrofit
One hangar ditched riveting for dual‑sided laser weld. They saw cycle time shrink noticeably. There were far fewer fasteners. Post‑weld prep demands dropped dramatically. Conversion was smooth thanks to BOGONG Laser’s on‑site setup crew.
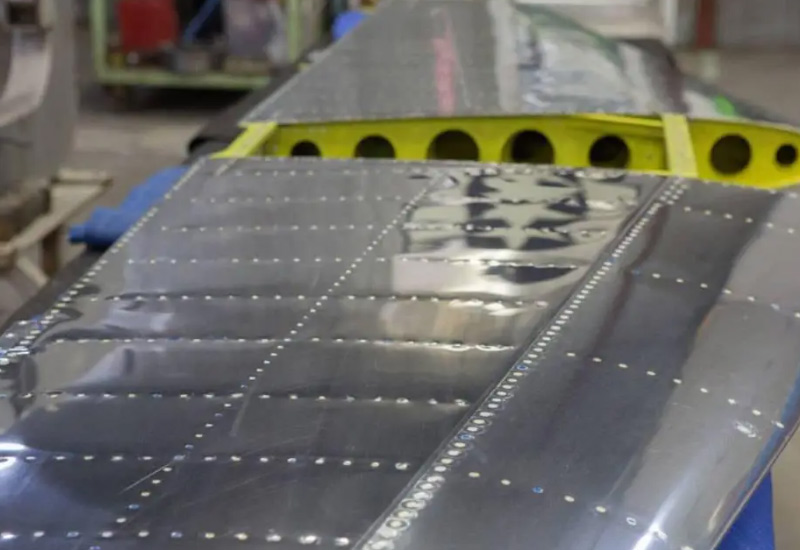
Regional Jet Skin Upgrade
A turboprop overhaul team needed small‑batch runs of custom‑length skins. They loaded presets for latest‑grade alloy. They logged interpass temperatures and pool dynamics. They ran flawless batches with zero rejects or delays. That’s uptime you can bank on.
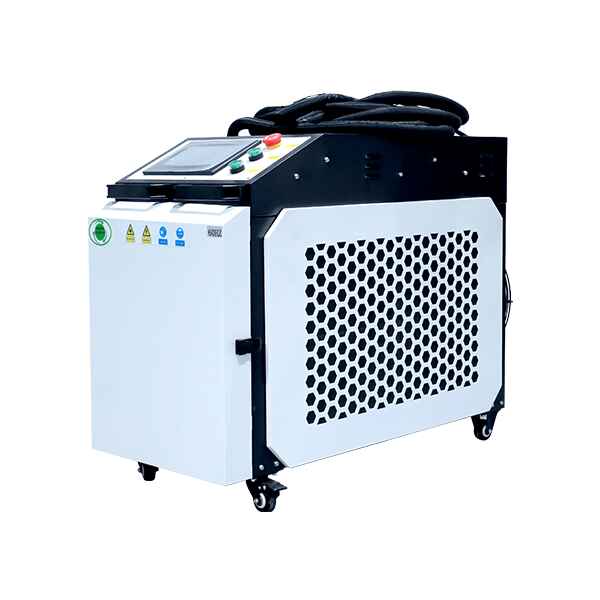
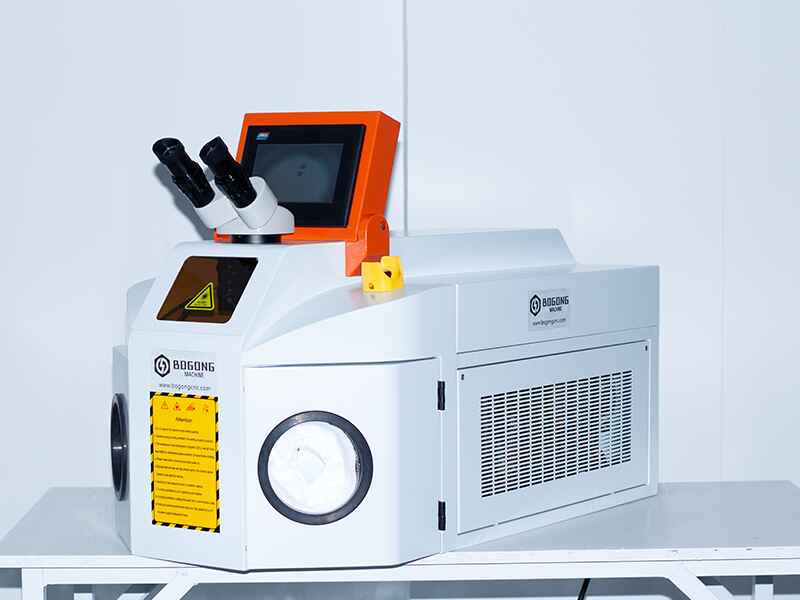
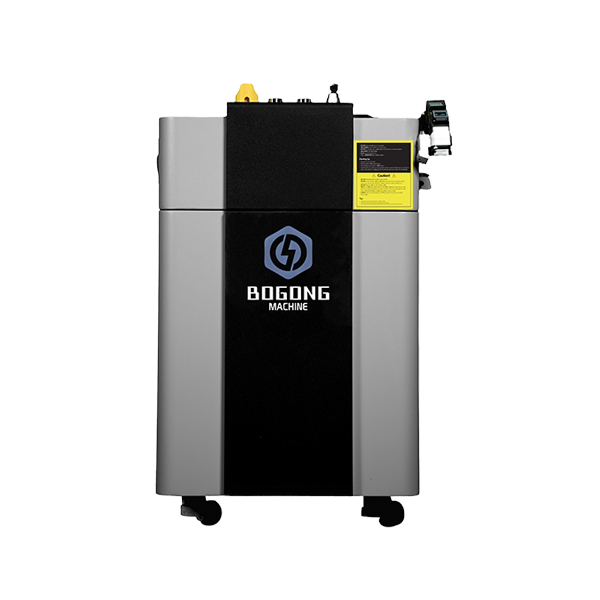
Picking Your Fit: Handheld, Mini CCD, or Gantry
Not every shop needs a gantry. Sometimes you need on‑wing fixes. Other times you tackle sub‑assemblies.
Check out our Handheld Laser Welding Machine for mobile touch‑ups.
The Mini Laser Welding Machine with CCD brings vision‑assisted precision to jigs and small skins.
Our 3 in 1 Handheld Laser Welder covers welding, cutting, and cleaning in one box.
Why BOGONG Laser Rocks
You want a Laser Welding Machine Manufacturer who truly gets aerospace. That’s us. We’re a top Laser Welding Machine Factory with global certifications—CE, ISO9001, SGS, FDA, and BV. We speak your language—English, Deutsch, Español—and ship to fleets in dozens of countries, serving thousands of clients.
OEM/ODM Know‑How
Need a custom head? We machine optical mounts in‑house. Want your PLC to sync with MES? We code it. We rig chillers. We test mean time between failures. We run factory and site acceptance trials. You get a turnkey cell, not just a bare frame.
Certified Quality Workflow
Every machine cruises through IQ/OQ/PQ cycles. We log design‑to‑performance metrics. You get a full QA dossier that keeps your auditors—and your ISO team—happy.
Getting Started
If you’ve wrestled with spatter, warping, or slow cycles, give us a shout. Fill out the contact form on BOGONG Laser and let’s chat about ramping up your line without breakouts or rework.