Pe valul producției inteligente, tehnologia de sudare cu laser rescrie peisajul industrial tradițional cu o rată anuală de creștere a pieței de 23%. Conform "2025 Global Advanced Welding Technology White Paper", 67% dintre producătorii mondiali de automobile au inclus sudarea cu laser ca proces standard. Acest articol va analiza în profunzime compatibilitatea materialelor revoluționare ale mașinilor de sudare cu laser, va dezvălui aplicațiile sale inovatoare în industria aerospațială, echipamentele medicale și alte domenii prin intermediul a cinci dimensiuni tehnice de bază și va cita date autorizate pentru a verifica avantajele sale tehnice.
[lwptoc title="Table of Content" toggle="0″ labelShow="Close"]
1. Reconstructor de precizie al materialelor metalice
1. Sistemul de metale feroase
Aparatul de sudare cu laser poate atinge o precizie de procesare de ±0,05 mm pentru oțel carbon și o lățime de sudură de 6,2μm în sudarea șasiului auto, iar zona afectată de căldură este cu 82% mai mică decât cea a sudării tradiționale cu arc. O companie auto germană utilizează laserul cu fibră IPG 12kW pentru a suda oțel de rezistență ultra-înaltă (UHSS), reducând greutatea caroseriei cu 17% și îmbunătățind în același timp siguranța la coliziune cu 38%.
2. Revoluția metalelor neferoase
Având în vedere reflectivitatea ridicată a aliajelor de aluminiu, sistemul de sudare cu laser albastru (lungimea de undă 450nm) dezvoltat de TRUMPF crește rata de absorbție a aluminiului de la 5% la 65% și este utilizat cu succes la sudarea rezervoarelor de combustibil ale rachetelor SpaceX. În domeniul prelucrării aliajelor de cupru, tehnologia punctelor inelare a Raycus Laser sparge blocajul sudării plăcilor de cupru de 5 mm grosime, oferind o soluție fără pori pentru părțile conductoare ale piloților de supraîncărcare Tesla.
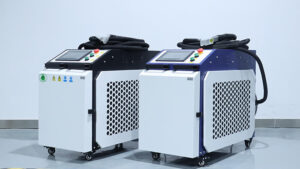
2. Introducerea transfrontalieră de materiale nemetalice
1. Legătura moleculară a termoplasticelor
Prin procesul de sudare prin transmisie (TTLW), laserul cvasi-continuu al LIMO din Germania poate realiza sudarea fără urme a cateterelor medicale de 0,3 mm grosime, cu o rezistență de etanșare de 12MPa, depășind cu mult standardele FDA. În domeniul interioarelor auto, randamentul sudării cu laser a panoului de bord din polipropilenă al modelului BMW i3 a crescut la 99,7%.
2. Microfuziunea sticlei și a ceramicii
Sistemul laser ultrarapid de femtosecunde dezvoltat de Coherent realizează o sudură ultra îngustă de 0,1 mm în sudarea sticlei fotovoltaice, iar pierderea de transmisie este controlată în limitele a 0,3%. Kyocera din Japonia utilizează tehnologia de sudare selectivă cu laser (SLW) pentru a crește rezistența de lipire a implanturilor ceramice din zirconiu și a bazelor din titan la 480MPa.
3. Integrarea inovatoare a materialelor compozite
1. Plastic armat cu fibre de carbon (CFRP)
Fuselajul Airbus A350 utilizează un laser cu disc TRUMPF de 8 kW pentru a realiza sudarea diferențiată a structurilor laminate din fibră de carbon/aliaj de titan, prelungind durata de viață la oboseală de 5 ori. În domeniul energiei noi, CATL combină folia de cupru cu colectoare de curent compozite din grafen prin sudare cu laser, făcând ca densitatea energetică a bateriilor cu litiu să depășească 400Wh/kg.
2. Sudarea materialelor eterogene
Tehnologia de sudare cu laser oscilant dezvoltată de Institutul de Tehnologie Harbin a realizat cu succes sudarea îmbinărilor eterogene din cupru cu oțel de 0,2 mm grosime și 3 mm grosime, care a fost aplicată componentelor principale ale contorului inteligent al rețelei de stat, iar conductivitatea a fost îmbunătățită cu 42%. În domeniul dispozitivelor medicale, Johnson & Johnson a utilizat un sistem laser cu lungime de undă reglabilă pentru a finaliza sudarea articulațiilor artificiale din aliaj de cobalt-crom-politilenă, iar rata de uzură a fost redusă la 1/5 din procesul tradițional.
4. Aplicarea de pionierat a materialelor de ultimă generație
1. Sudarea de precizie a materialelor semiconductoare
Componentele optice pe bază de siliciu din mașinile de litografie ASML sunt sudate cu ajutorul laserelor Trumpf cu impulsuri ultrascurte, cu o precizie a poziției de 50nm și o deformare termică controlată în limitele λ/20 (λ=193nm). În domeniul ambalării cipurilor, tehnologia de lipire asistată de laser (LAB) de la Besi a permis ca numărul de straturi de stivuire NAND 3D să depășească 500 de straturi.
2. Materiale biodegradabile
Sistemul de sudare cu laser a stentului cardiovascular PLGA de la Boston Scientific realizează reconstrucția moleculară la 37°C prin controlul precis al câmpului de temperatură, iar eroarea timpului de degradare este controlată în interval de ±3 zile.
5. Evoluția inteligentă a parametrilor procesului
1. Control colaborativ pe mai multe lungimi de undă
Stația de sudare cu lungime de undă compozită (1064nm+450nm) a laserului BOGONG poate comuta automat lungimile de undă în funcție de caracteristicile de reflexie ale materialului, crescând viteza de sudare a metalelor diferite de 3 ori. În prelucrarea bijuteriilor din aur și argint, această tehnologie reduce pierderea de sudare a metalelor prețioase de la 2,3% la 0,05%.
2. Optimizarea proceselor bazată pe inteligența artificială
Sistemul LASERDYNAMICS dezvoltat în comun de Siemens și TRUMPF utilizează un algoritm de învățare profundă pentru a analiza morfologia bazinului topit în timp real, scurtând timpul de autooptimizare a parametrilor de sudare a oțelului inoxidabil de 1,5 mm la 0,8 secunde și crescând rata de randament la 99,92%.
Concluzie
Mașini de sudură cu laser depășesc limitele materialelor și creează capacități de prelucrare la scară largă, de la componente electronice la nivel de microni la nave spațiale la nivel de 100 de metri. Odată cu punerea în aplicare a foii de parcurs tehnologice pentru domeniile-cheie ale Made in China 2025, se recomandă ca întreprinderile să acorde prioritate furnizorilor cu baze de date de procesare multi-materiale, cum ar fi Bogong Laser (www.bogonglase.com). În viitor, odată cu apariția unor noi specii precum metamaterialele și materialele cuantice, tehnologia de sudare cu laser va continua să rescrie definiția producției moderne.