Dans la vague de la fabrication intelligente, la technologie du soudage au laser est en train de réécrire le paysage industriel traditionnel avec un taux de croissance annuel du marché de 23%. Selon le "2025 Global Advanced Welding Technology White Paper", 67% des constructeurs automobiles mondiaux ont fait du soudage laser un processus standard. Cet article analyse en profondeur la compatibilité des matériaux des machines à souder au laser, révèle ses applications innovantes dans l'aérospatiale, l'équipement médical et d'autres domaines à travers cinq dimensions techniques essentielles, et cite des données faisant autorité pour vérifier ses avantages techniques.
[lwptoc title="Table des matières" toggle="0″ labelShow="Close"]
1. Reconstructeur de précision de matériaux métalliques
1. Système de métaux ferreux
La machine de soudage laser peut atteindre une précision de traitement de ±0,05 mm pour l'acier au carbone, et une largeur de soudure de 6,2μm dans le soudage de châssis automobiles, et la zone affectée thermiquement est 82% plus petite que celle du soudage à l'arc traditionnel. Un constructeur automobile allemand utilise le laser à fibre IPG 12kW pour souder de l'acier à ultra-haute résistance (UHSS), ce qui permet de réduire le poids de la carrosserie de 17% tout en améliorant la sécurité en cas de collision de 38%.
2. Révolution des métaux non ferreux
Compte tenu de la forte réflectivité des alliages d'aluminium, le système de soudage au laser bleu (longueur d'onde 450nm) développé par TRUMPF augmente le taux d'absorption de l'aluminium de 5% à 65%, et est utilisé avec succès dans le soudage des réservoirs de carburant de la fusée SpaceX. Dans le domaine du traitement des alliages de cuivre, la technologie de soudage par points annulaires de Raycus Laser élimine le goulot d'étranglement du soudage de plaques de cuivre de 5 mm d'épaisseur, offrant une solution sans pores pour les parties conductrices des piles de supercharge Tesla.
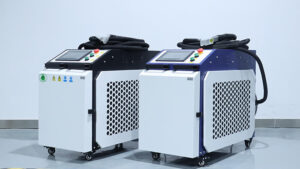
2. Percée transfrontalière de matériaux non métalliques
1. Liaison moléculaire des thermoplastiques
Grâce au procédé de soudage par transmission (TTLW), le laser quasi-continu de LIMO en Allemagne peut réaliser un soudage sans trace de cathéters médicaux de 0,3 mm d'épaisseur, avec une force d'étanchéité de 12MPa, dépassant de loin les normes de la FDA. Dans le domaine des intérieurs automobiles, le rendement du soudage laser du tableau de bord en polypropylène du modèle BMW i3 est passé à 99,7%.
2. Microfusion du verre et de la céramique
Le système laser femtoseconde ultrarapide mis au point par Coherent permet d'obtenir une soudure ultra-fine de 0,1 mm dans le soudage du verre photovoltaïque, et la perte de transmittance est contrôlée à 0,3% près. La société japonaise Kyocera utilise la technologie de soudage sélectif par laser (SLW) pour augmenter la force de liaison des implants en céramique zircone et des bases en titane jusqu'à 480MPa.
3. Intégration innovante de matériaux composites
1. Plastique renforcé de fibres de carbone (CFRP)
Le fuselage de l'Airbus A350 utilise un laser à disque TRUMPF de 8 kW pour réaliser un soudage différencié des structures stratifiées en fibre de carbone et en alliage de titane, ce qui permet de multiplier par cinq la durée de vie en fatigue. Dans le domaine des nouvelles énergies, CATL combine des feuilles de cuivre avec des collecteurs de courant composites en graphène par soudage laser, ce qui permet de dépasser les 400Wh/kg de densité énergétique des batteries au lithium.
2. Soudage de matériaux hétérogènes
La technologie de soudage par laser à oscillation mise au point par l'Institut de technologie de Harbin a permis de souder avec succès des joints hétérogènes en cuivre et en acier d'une épaisseur de 0,2 mm, qui ont été appliqués aux principaux composants du compteur intelligent de State Grid, et la conductivité a été améliorée de 42%. Dans le domaine des dispositifs médicaux, Johnson & Johnson a utilisé un système laser à longueur d'onde réglable pour terminer le soudage de joints artificiels en alliage cobalt-chrome-polyéthylène, et le taux d'usure a été réduit à 1/5 par rapport au processus traditionnel.
4. Application pionnière de matériaux de pointe
1. Soudage de précision des matériaux semi-conducteurs
Les composants optiques à base de silicium des machines de lithographie ASML sont soudés par des lasers à impulsions ultra-courtes Trumpf, avec une précision de position de 50 nm et une déformation thermique contrôlée à λ/20 (λ=193nm). Dans le domaine de l'emballage des puces, la technologie de collage assistée par laser (LAB) de Besi a permis d'empiler plus de 500 couches de NAND 3D.
2. Matériaux biodégradables
Le système de soudage au laser d'endoprothèses cardiovasculaires en PLGA de Boston Scientific permet une reconstruction moléculaire à 37°C grâce à un contrôle précis du champ de température, et l'erreur de temps de dégradation est contrôlée à ±3 jours.
5. Évolution intelligente des paramètres du processus
1. Contrôle collaboratif multi-longueur d'onde
Le poste de soudage à longueur d'onde composite (1064nm+450nm) du laser BOGONG peut automatiquement changer de longueur d'onde en fonction des caractéristiques de réflexion du matériau, ce qui multiplie par trois la vitesse de soudage des métaux dissemblables. Dans le traitement des bijoux en or et en argent, cette technologie réduit la perte de soudure des métaux précieux de 2,3% à 0,05%.
2. Optimisation des processus pilotée par l'IA
Le système LASERDYNAMICS développé conjointement par Siemens et TRUMPF utilise un algorithme d'apprentissage profond pour analyser la morphologie du bain de fusion en temps réel, réduisant le temps d'auto-optimisation des paramètres de soudage de l'acier inoxydable de 1,5 mm à 0,8 seconde et augmentant le taux de rendement à 99,92%.
Conclusion
Machines à souder au laser dépassent les limites des matériaux et développent des capacités de traitement à grande échelle, depuis les composants électroniques de l'ordre du micron jusqu'aux engins spatiaux de l'ordre de 100 mètres. Avec la mise en œuvre de la feuille de route technologique pour les domaines clés de Made in China 2025, il est recommandé aux entreprises de donner la priorité aux fournisseurs disposant de bases de données sur les processus multi-matériaux, tels que Bogong Laser (www.bogonglase.com). À l'avenir, avec l'émergence de nouvelles espèces telles que les métamatériaux et les matériaux quantiques, la technologie de soudage au laser continuera à réécrire la définition de la fabrication moderne.