Dans le contexte de l'ère industrielle 4.0, la technologie de nettoyage au laser est devenue l'un des équipements de base pour la mise à niveau de l'industrie manufacturière en raison de ses caractéristiques sans contact, non destructives et hautement respectueuses de l'environnement. Selon le "2024-2030 China Laser Cleaning Market Application Trend Report", le taux de croissance annuel composé de ce domaine atteindra 18% au cours des cinq prochaines années. Cependant, face à la complexité des modèles d'équipement et à la sélection des fournisseurs sur le marché, comment répondre précisément aux besoins et obtenir des retours sur investissement à long terme ? Cet article procède à une analyse systématique sous deux angles : les éléments essentiels de la sélection des équipements et la stratégie d'évaluation des fournisseurs.
[lwptoc title="Table des matières" toggle="0″ labelShow="close" labelHide="隐藏"]
1. Éléments essentiels de la machine de nettoyage au laser sélection
1. Clarifier les besoins en matière de nettoyage : les scénarios d'application déterminent les types d'équipement
Les performances de la machine de nettoyage laser doivent être parfaitement adaptées à l'objet à nettoyer. Par exemple, les appareils portatifs conviennent à la restauration de reliques culturelles et au nettoyage de moules sur de petites surfaces, tandis que les systèmes intégrés automatisés conviennent aux scénarios de production en continu tels que les lignes de soudage automobile. Trois indicateurs doivent être clarifiés avant la sélection :
- Compatibilité avec les matériaux : Le dérouillage des métaux nécessite un laser pulsé de plus de 500 W, tandis que le nettoyage des plaquettes de semi-conducteurs requiert un laser continu de faible puissance.
- Type de pollution : La couche d'oxyde nécessite une densité d'énergie élevée (>15J/cm²), et la pollution par les hydrocarbures convient aux équipements à courte longueur d'onde (1064 nm).
- Exigences en matière d'efficacité : La vitesse de nettoyage de l'équipement manuel est d'environ 1 cm²/s, et le système automatisé peut atteindre 20 cm²/s.
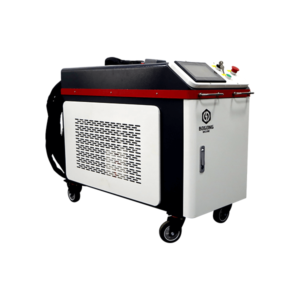
2. Analyse des paramètres de performance : Les indicateurs techniques déterminent l'effet de nettoyage
La puissance n'est pas le seul critère, et les paramètres quadridimensionnels doivent être évalués de manière exhaustive :
- Qualité du faisceau (valeur M²) : <1,3 peut assurer un nettoyage fin (tel que la réparation de la texture du moule)
- Fréquence d'impulsion : 20-100 kHz pour équilibrer la vitesse de nettoyage et le contrôle des zones affectées par la chaleur.
- Précision du balayage : la précision de ±0,01 mm répond aux besoins de nettoyage des pales de moteurs d'avion.
- Protection de la sécurité : Le niveau de protection IP54 et la certification de sécurité laser de classe 1 sont requis.
3. Bilan coût-efficacité : modèle d'investissement sur l'ensemble du cycle de vie
Éléments de coût | Matériel de sablage (5 ans) | Équipement de nettoyage au laser (5 ans) |
---|---|---|
Investissement initial | $27,000 | $110,000 |
Coût des consommables | $60,000 | $5 000 (électricité) |
Taxe de gestion de la protection de l'environnement | $40,000 | $0 |
Coût total | $135,000 | $116,000 |
2. Cinq critères d'or pour l'évaluation des fournisseurs
1. Puissance technique en matière de R&D : présentation des brevets et capacité d'innovation
Les fournisseurs de haute qualité doivent avoir :
- Droits de propriété intellectuelle indépendants :
- Coopération industrie-université-recherche :
- Capacité d'itération technique : fournir des solutions de mise à niveau modulaire (telles que la conception de coupleurs de fibres remplaçables).
2. Système de qualité de la production : double garantie des matières premières aux produits finis
Les fournisseurs doivent être inspectés sur place :
- Source des composants de base : Raycus Laser > American IPG Laser > solutions alternatives nationales
- Normes de contrôle des processus : Le taux de qualification de la ligne de production certifiée ISO 9001 doit être > 99,3%
- Configuration de l'équipement d'essai : analyseur de la qualité du faisceau et profileur 3D requis
3. Couverture du réseau de services : vérification de la capacité de soutien sur l'ensemble du cycle
Indicateurs clés pour l'évaluation des capacités de service :
- Temps de réponse : 4 heures sur place dans les villes de premier rang, 12 heures pour les villes de second rang.
- Taux de réserve des pièces détachées : Le taux d'adéquation des stocks de consommables communs (tels que les lentilles de mise au point) doit être de >95%
4. Cas d'application dans l'industrie : valorisation de l'expérience pratique
Inspections clés :
- Cas de réussite dans le même secteur : Les fournisseurs qui coopèrent avec Volkswagen/Tesla sont privilégiés dans le secteur automobile
- Capacités de résolution de scénarios complexes : par exemple, le projet de nettoyage au laser des boîtes de vitesses des trains à grande vitesse du groupe CRRC.
- Dossiers de développement personnalisés : Les anciens documents de conception de solutions non standard doivent être fournis.
5. Modalités de la coopération commerciale : prévention et contrôle des risques et protection des droits
Le contrat doit être clair :
- Conditions de garantie de performance : Si l'efficacité du nettoyage n'atteint pas la valeur promise, 0,5% sera déduit quotidiennement.
- Ratio d'échelonnement des paiements : Il est recommandé d'adopter un modèle de paiement échelonné de 3:4:2:1.
- Propriété intellectuelle : Les technologies développées conjointement doivent clarifier le mécanisme de partage des brevets.
Conclusion
Le choix des machines de nettoyage au laser n'est pas seulement une décision technique, mais aussi un investissement stratégique. Les entreprises doivent établir un modèle d'évaluation quadridimensionnel "demande-technologie-coût-service" et donner la priorité aux fournisseurs ayant des capacités de service de la chaîne de valeur complète, tels que JINAN BOGONG MACHINERY CO.,LTD (avec des qualifications militaires). Avec la mise en œuvre des normes de production propre "Made in China 2025", ce n'est qu'en sélectionnant avec précision et en coordonnant avec des fournisseurs de haute qualité que nous pourrons prendre le dessus en améliorant la qualité, l'efficacité et le développement durable.