Technische Vorteile des Laserschneidens
Hier erfahren Sie, warum Laser mechanische Werkzeuge übertreffen:
Hohe Präzision und Reproduzierbarkeit
Laser werden nicht stumpf. Sie treffen die gleiche Toleranz bei Teil #1 oder Teil #10.000. Diese Art der Konsistenz von Charge zu Charge verringert die Ausschussrate.
Minimale Wärmeeinflusszone (HAZ)
Mit der Impulssteuerung halten Sie die WEZ unter 50 µm. Das bedeutet keine Mikrorisse und weniger Spannungsabbau nach der Bearbeitung. Ihre Teile bleiben stabiler.
Material Vielseitigkeit
Von biostabilen Polymeren bis hin zu Superlegierungen - ein einziger Laserkopf kann sie alle bearbeiten. Wechseln Sie Schneidparameter in Sekundenschnelle - ohne Werkzeugwechsel oder Kalibrierungsläufe.
Fallstudien
Werfen wir einen Blick hinter die Kulissen von zwei Fabriken, in denen Laserschneiden groß geschrieben wird:
Herstellung von ultra-dünnen Kathetern
Ein medizintechnischer OEM benötigte 0,02 mm Nitinolschläuche für Neurokatheter. Mechanische Methoden konnten keine konsistenten Schlitze liefern. Sie installierten eine 5050 Faserlaser-Schneidemaschine von BOGONG Laser. Das Ergebnis? 98% Ausbeute beim ersten Durchlauf und keine Grate. Die Produktionszeit wurde um 30% verkürzt und die Nacharbeit bei der Qualitätskontrolle reduziert.
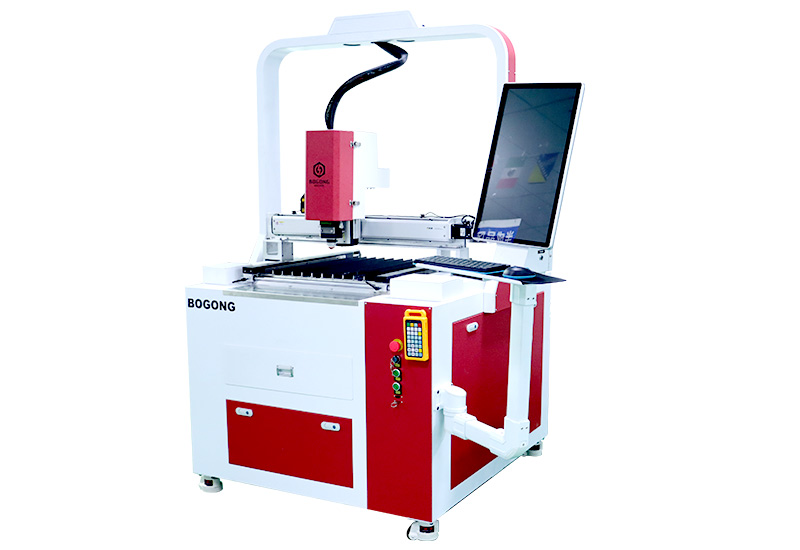
Maßgeschneiderte orthopädische Platten
Ein orthopädisches Startup-Unternehmen benötigte maßgeschneiderte Knochenplatten aus Ti6Al4V mit komplizierten Schraubenlöchern. Sie gewannen eine Faserlaser-Schneidemaschine Combo, die sowohl Bleche als auch Rohre (Tube-to-Plate-Nesting) verarbeitet. Die Ingenieure wählten eine Spotgröße von 25 µm. Die Platten passen perfekt, keine manuelle Nachbearbeitung, und das Feedback der Chirurgen war hervorragend.
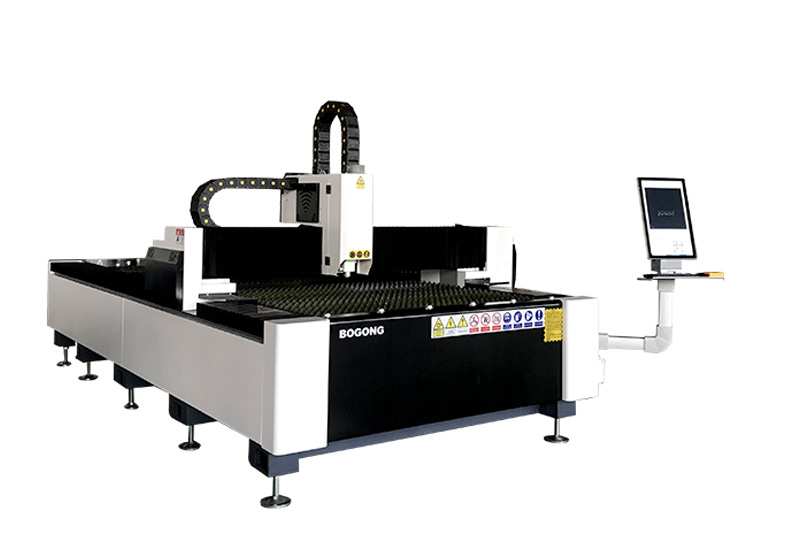
Warum Laserschneiden die Präzision in der Produktion medizinischer Geräte vorantreibt
Beim Laserschneiden in der Fertigung medizinischer Geräte geht es nicht nur um Geschwindigkeit. Sie bekommen:
Submikron-Genauigkeit. Laser fokussieren bis zu einem Strahldurchmesser von weniger als 50 µm.
Wiederholbare Schnitte. Charge für Charge entspricht jedes Teil den CAD-Spezifikationen.
Reinraumfreundlicher Prozess. Er ist berührungslos und nahezu staubfrei - genau das, was Ihr Reinraum der Klasse ISO 5 braucht.
Außerdem können Sie komplexe Formen - kurvige Stentgitter oder Mikroventile - ohne mechanische Belastung schneiden. Kurz gesagt, das Laserschneiden ist die Antwort auf die größten Probleme der Hersteller medizinischer Geräte: Anforderungen an die Rückverfolgbarkeit, enge Toleranzen und schnelle Durchlaufzeiten.
Wichtige Anwendungsfälle für das Laserschneiden in der Medizintechnik
Hersteller vertrauen dem Laserschneiden in einer Reihe von Szenarien. Hier ist eine Momentaufnahme:
Katheter und Stents
Sie brauchen ultradünne Wände, die trotzdem ihre Form behalten. Beim Laserschneiden werden hochnickelhaltige Legierungen (wie Nitinol) bis auf 0,02 mm Dicke mit einer Toleranz von ±0,005 mm heruntergeschnitten. Diese Konsistenz bedeutet, dass sich jeder von Ihnen gelieferte Stent in vivo gleich verhält.
Chirurgische Instrumente
Denken Sie an Pinzettenspitzen mit rasiermesserscharfen Kanten und ohne Grate. Beim Laserschneiden werden rostfreie Stahlbleche (0,3-3 mm) bearbeitet und anschließend elektropoliert. Das Ergebnis sind Instrumente, die durch das Gewebe gleiten, und das merken die Chirurgen.
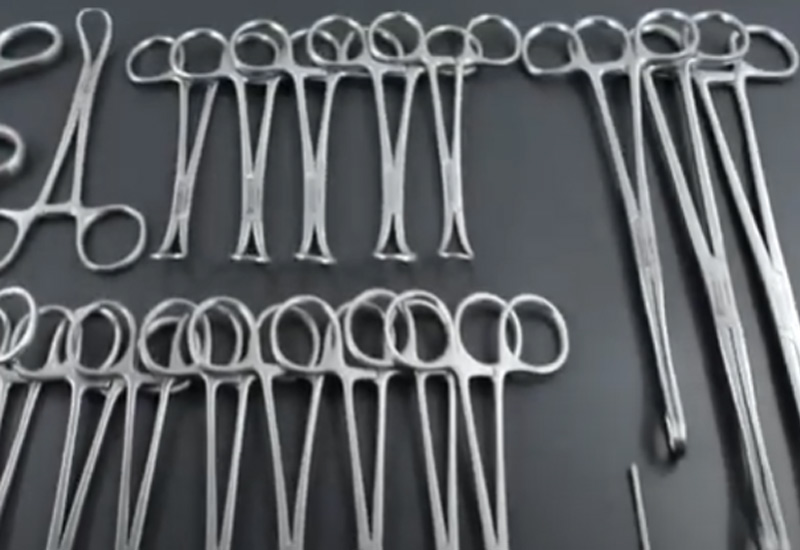
Diagnostische Komponenten
Für mikrofluidische Chips und Sensorgehäuse werden häufig Polymere wie PEEK verwendet. Laser schneiden Kanäle von 0,1 mm Breite, ohne die Wände zu schmelzen. Das ist entscheidend, wenn man Blutproben in winzigen Mengen analysieren will.
Zukünftige Trends im medizinischen Laserschneiden
Das Laserschneiden wird sich nicht verlangsamen - im Gegenteil, die Miniaturisierung und Automatisierung wird noch weiter vorangetrieben:
Mikrofabrikation und Miniaturisierung
Achten Sie auf Strukturgrößen unter 10 µm und hybride Laser-Etch-Kombinationen. Das ist der Schlüssel für Implantate und Bio-Chips der nächsten Generation.
Intelligente Fabriken und digitale Zwillinge
Echtzeitüberwachung, KI-gesteuerte Parameteranpassungen und vorausschauende Wartung sind bereits in Pilotanlagen im Einsatz. Bald wird sich Ihre Schneidzelle selbst optimieren.
Werksnormen und deren Einhaltung
Ihre Anlage muss CE-, FDA-, ISO9001- und SGS-Audits bestehen. Suchen Sie nach:
Kühlung im geschlossenen Kreislauf. Vermeiden Sie Kondensation in Umgebungen der Klasse 100.
HEPA-Filter. Hält den Feinstaub unter Kontrolle.
Rückführbare Servoantriebe. Ermöglicht digitale Zwillingseinstellungen und vollständige Chargenrückverfolgbarkeit.
BOGONG Laser, eine zertifizierte Fabrik für Laserschneidmaschinen, integriert alle oben genannten Aspekte.
Wie der BOGONG-Laser die Anforderungen an medizinische Geräte erfüllt
Als ein führender Hersteller von Laserschneidmaschinen verbindet BOGONG Laser Forschung und Entwicklung mit Service:
Kundenspezifische Lösungen von einem zuverlässigen Hersteller
Ganz gleich, ob Sie Mikrogitterschnitte oder schwere Platten benötigen, sie konfigurieren Ihre Faserleistung, Impulsbreite und Optik. Sie erhalten eine schlüsselfertige Anlage.
Weltweite Unterstützung und OEM/ODM-Optionen
Mit Kunden in über 160 Ländern bedeutet der mehrsprachige Support von BOGONG, dass Sie nie feststecken. BOGONG bietet ein vollständiges OEM/ODM-Angebot für das Branding oder die Integration von Steuerungssystemen.
Schlussfolgerung
Das Laserschneiden in der Medizintechnik ist keine Eintagsfliege. Es ist die Methode der Wahl für alle, die Wert auf Präzision, Sauberkeit und kurze Zykluszeiten legen. Von ultradünnen Stents bis hin zu lebensrettenden Implantaten - Laser liefern wiederholbare, gratfreie Teile, die für die Zufriedenheit der Behörden und die Sicherheit der Patienten sorgen. Wenn Sie bereit sind, Kosten zu senken, den Ertrag zu steigern und den sich entwickelnden Vorschriften einen Schritt voraus zu sein, sollten Sie mit einem bewährten Hersteller von Laserschneidmaschinen wie BOGONG Laser zusammenarbeiten. Wir konfigurieren das richtige System, integrieren es in Ihren Reinraum und unterstützen Sie, wo immer Sie tätig sind.